The production of knee pads contributes a significant amount to carbon emissions and environmental footprint. It’s time for a change. In this post, we’ll explore innovative strategies and sustainable practices that can drastically reduce the carbon footprint associated with knee pad manufacturing. From eco-friendly materials to energy-efficient production processes, every step counts in our mission to create a greener and cleaner future for protective gear. Join us as we delve into the exciting advancements and initiatives revolutionizing the industry towards sustainability.
Table of Contents
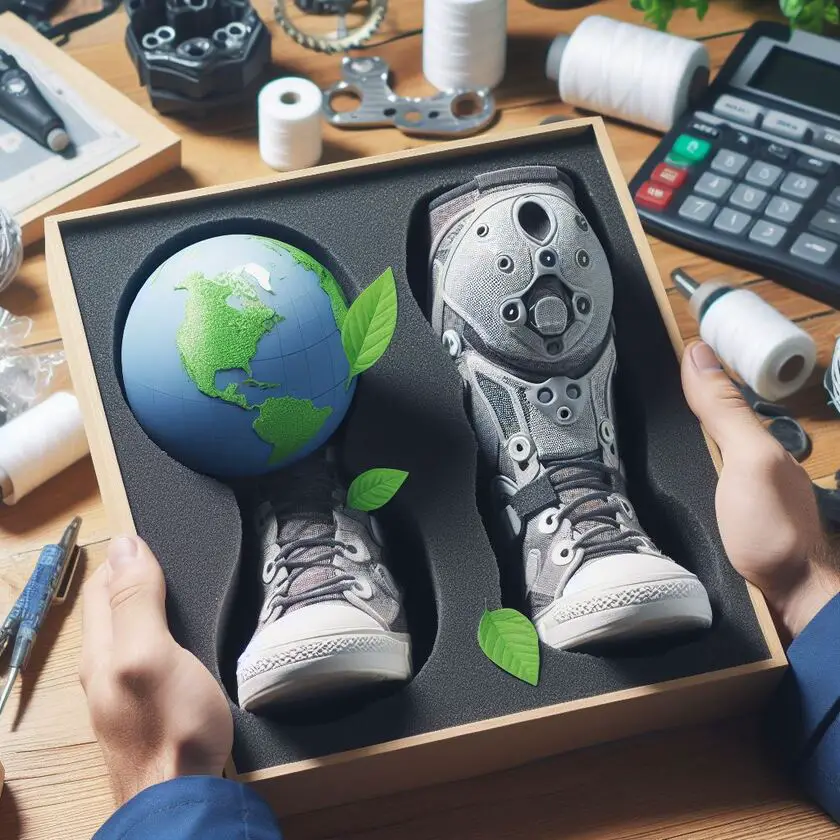
Key Takeaways
- Implementing energy-efficient manufacturing processes and utilizing sustainable materials can significantly reduce the environmental impact of knee pad production.
- Identifying and addressing carbon footprint hotspots, such as raw material extraction and transportation, is crucial in effectively reducing the overall carbon footprint of knee pad production.
- Embracing innovative approaches, such as 3D printing and recycled materials, can lead to substantial reductions in carbon emissions during knee pad manufacturing.
- Collaborative efforts among manufacturers, suppliers, and industry stakeholders are essential for implementing sustainable practices and collectively reducing the carbon footprint of knee pad production.
- Ethical considerations, including fair labor practices and responsible sourcing, should be integrated into knee pad production to ensure a holistic approach to sustainability.
- Investing in funding for sustainability research and development can drive advancements in eco-friendly materials and processes, ultimately contributing to lower carbon emissions in knee pad production.
- It’s important to acknowledge the limitations in reducing carbon footprint in knee pad production and continuously strive for innovative solutions to overcome these challenges.
Reducing Carbon Footprint in Knee Pad Production
Reduce your knee pad’s carbon footprint with eco-friendly materials like recycled fabrics and plant-based foams. Power production with renewables, minimize waste, and design for easy recycling. Be transparent about your efforts and collaborate for a greener future!
Environmental Impact of Knee Pad Production
Carbon Footprint Assessment
The first step is conducting a comprehensive analysis of carbon emissions. This involves identifying sources of carbon footprint, such as energy consumption during manufacturing and transportation. Implementing tools such as life cycle assessment to measure and monitor greenhouse gas emissions allows companies to track their progress and make informed decisions about reducing emissions.
Greenhouse Gas Emissions
To minimize methane and nitrous oxide emissions and reduce the total carbon footprint from manufacturing processes, companies can invest in technologies that capture or reduce these gases. Utilizing energy-efficient technologies like solar power or LED lighting helps decrease overall greenhouse gas emissions from the production process. Implementing strategies to lower the release of fluorinated gases, commonly used in cooling systems, contributes to a significant reduction in environmental impact.
Life Cycle Analysis
Evaluating environmental impacts at every stage of knee pad production is crucial for understanding the product’s overall sustainability. Conducting a life cycle analysis involves assessing the cradle-to-grave environmental effects of knee pad materials, including raw material extraction, manufacturing, distribution, use phase, and end-of-life disposal. Identifying opportunities for reducing environmental burdens throughout the product’s life cycle enables manufacturers to implement targeted measures for sustainable improvement.
Carbon Footprint Hotspots in Production
Material Sourcing
One of the critical areas to address is material sourcing. By exploring alternatives to traditional materials with high carbon footprints, such as coal, and opting for sustainable and eco-friendly options, manufacturers can significantly minimize the environmental impact. It’s essential to prioritize responsible sourcing practices, ensuring that the materials used have minimal negative effects on the environment, including life cycle assessment and emission factors.
By selecting suppliers who adhere to sustainable harvesting and extraction methods, companies can further reduce their carbon hotspot related to material sourcing. For instance, choosing recycled or organic fabrics over conventional products not only lowers carbon emissions but also contributes positively towards waste reduction.
Manufacturing Processes
Optimizing manufacturing processes plays a pivotal role in mitigating the high carbon contributors associated with knee pad production. Implementing lean manufacturing principles helps minimize waste generation while reducing energy consumption during various stages of production. Moreover, incorporating innovative techniques like renewable energy sources aids in lowering overall carbon emissions.
By embracing environmentally friendly practices at every stage of manufacturing – from raw material processing to final assembly – companies can effectively curtail their contribution to high carbon products.
Packaging and Distribution
In the realm of packaging and distribution, using minimal packaging materials is crucial for reducing waste and cutting down on carbon emissions. Optimizing transportation logistics also plays a significant role in decreasing the overall carbon footprint associated with product distribution. Exploring eco-friendly packaging solutions further enhances sustainability efforts by promoting responsible product delivery practices, operations, and life cycle assessment.
Strategies for Carbon Footprint Reduction
Sustainable Materials
One effective strategy is to use sustainable materials. This involves exploring renewable and biodegradable materials for construction, such as bamboo fibers or organic cotton. These materials have a lower environmental impact throughout their life cycle compared to traditional synthetic materials. By prioritizing the use of these sustainable alternatives and conducting a life cycle assessment, knee pad manufacturers can significantly reduce their carbon footprint and equivalent emissions.
Investing in research and development of sustainable material alternatives is crucial for finding low carbon alternatives that maintain the quality and durability expected from knee pads. For example, companies can experiment with innovative plant-based polymers that offer similar performance characteristics to traditional petroleum-based plastics but with reduced environmental impact.
Energy Efficiency
Another key strategy for carbon footprint reduction in knee pad production is focusing on energy efficiency. Manufacturers can adopt energy-efficient equipment and machinery, reducing the overall energy consumption during the manufacturing process. Implementing energy management systems also plays a vital role in optimizing resource utilization by monitoring and controlling electricity usage at different stages of operations.
Integrating renewable energy sources into the production process further contributes to lowering the average carbon footprint and reductions of greenhouse gas emissions associated with knee pad manufacturing operations. For instance, utilizing solar panels or wind turbines to generate electricity helps minimize reliance on fossil fuels, leading to a more environmentally friendly production process.
Waste Management
Developing effective strategies for waste management is essential when aiming to reduce the carbon footprint in knee pad production. This includes implementing recycling programs within facilities and reusing waste generated during various stages of manufacturing. Minimizing landfill waste through efficient waste management practices ensures that fewer resources are wasted while simultaneously decreasing environmental harm caused by excessive landfill disposal.
Implementing a closed-loop system where materials are recycled back into the production process reduces both resource consumption and waste generation associated with knee pad manufacturing.
Innovative Approaches in Production
Design Innovation
Incorporating design features to minimize material usage and waste generation is crucial. By focusing on product design that enhances durability and longevity, knee pad manufacturers can significantly reduce their carbon footprint and equivalent emissions. For instance, using innovative materials that are both lightweight and durable can help achieve this goal. Embracing design innovation also involves creating environmentally friendly knee pads by utilizing recycled or biodegradable materials.
Technological Advancements
Leveraging advanced technologies plays a pivotal role in reducing the carbon footprint in knee pad production. Investing in automation and digitalization enables sustainable manufacturing practices by streamlining processes and minimizing energy consumption. Cutting-edge technologies provide precise control over resource consumption, leading to reduced emissions and carbon footprint during the production of knee pads. An example of this is implementing automated cutting processes that optimize material usage while minimizing waste generation.
Collaborative Efforts for Sustainability
Industry partnerships play a crucial role. By collaborating with suppliers committed to sustainable practices and materials sourcing, companies can ensure that the entire supply chain aligns with their sustainability goals. For example, partnering with suppliers who use recycled materials or renewable energy sources can significantly reduce the environmental impact of knee pad production.
Moreover, forming alliances with organizations dedicated to reducing carbon footprint and life cycle in manufacturing allows companies to stay updated on the latest sustainable technologies and best practices. These partnerships provide valuable insights into innovative methods for minimizing waste and optimizing energy usage throughout the production process.
Stakeholder engagement is another essential aspect of promoting sustainability in knee pad production. Involving employees, suppliers, and local communities in sustainability initiatives fosters a sense of collective responsibility towards environmental conservation. By communicating the importance of reducing carbon footprint in knee pad production, companies can inspire active participation from stakeholders at every level. This involvement may lead to creative ideas for implementing sustainable practices within the organization’s operations, carbon footprint.
Ethical Considerations in Production
Social Responsibility
Social responsibility plays a crucial role. Supporting fair labor practices and ethical working conditions throughout the supply chain is essential. This involves ensuring that workers involved in the production process are treated fairly and provided with safe working conditions. Contributing to community development initiatives related to environmental conservation is vital for reducing the overall impact on the environment, including carbon dioxide equivalent emissions.
Promoting social responsibility also means prioritizing the well-being of workers and local communities. Implementing sustainable practices not only benefits the environment but also positively impacts the health and livelihoods of those living near production facilities by reducing carbon dioxide equivalent emissions and carbon footprint.
Economic Viability
Evaluating cost-effective strategies for reducing carbon footprint without compromising quality is important. It’s crucial to demonstrate how sustainable practices can lead to financial benefits and reduce carbon dioxide equivalent emissions in knee pad production. By investing in efficient resource management, such as optimizing energy usage or minimizing waste generation, companies can achieve cost savings while maintaining product quality.
Furthermore, investigating opportunities for cost savings through efficient resource management ensures that economic viability remains a priority when implementing sustainable practices within knee pad production processes.
Funding for Sustainability Research
Seeking government grants or subsidies is crucial in reducing carbon footprint in knee pad production. These financial aids support eco-friendly manufacturing initiatives, reducing carbon dioxide equivalent emissions and making it easier to invest in sustainable technologies. By exploring funding opportunities, companies can conduct research and development aimed at implementing low-carbon production processes. For instance, a company may receive a grant to develop new materials with reduced environmental impact.
Investing in innovation is another vital aspect of reducing carbon footprint in knee pad production. Allocating resources towards researching and developing sustainable manufacturing solutions allows companies to create innovative technologies that contribute to lowering carbon emissions. This investment supports the continuous improvement of knee pad production methods that prioritize environmental sustainability by reducing carbon dioxide equivalent emissions. For example, a company might invest in advanced machinery that reduces energy consumption during the manufacturing process.
Limitations in Reducing Carbon Footprint
Technical Challenges
Addressing technical hurdles related to integrating sustainable materials into knee pad design is a significant challenge. Finding durable, eco-friendly materials that meet safety and performance standards can be complex. For instance, creating knee pads with sustainable padding material that still provides adequate protection while minimizing carbon footprint and carbon dioxide equivalent emissions requires extensive research and testing.
Overcoming obstacles associated with transitioning to low-carbon manufacturing processes presents another difficulty. Manufacturers may face challenges in sourcing low-carbon raw materials or implementing new production methods without compromising product quality or increasing costs. For example, adopting renewable energy sources for manufacturing can require substantial investment and infrastructure changes.
Navigating complexities involved in optimizing energy efficiency within existing production systems also poses a significant challenge. Upgrading machinery, reconfiguring workflows, and training staff on new processes are essential steps but can be resource-intensive. Implementing these changes while maintaining productivity levels demands careful planning and execution.
Market Constraints
Adapting products and marketing strategies to meet consumer demand for eco-friendly knee pads is crucial yet challenging. Consumers increasingly seek environmentally conscious products; however, effectively communicating the benefits of sustainable knee pads amid competitive market offerings, including their carbon footprint and carbon dioxide equivalent emissions, requires strategic branding and messaging.
Navigating regulatory requirements related to reducing carbon footprint and equivalent emissions in product manufacturing adds another layer of complexity for manufacturers. Compliance with environmental standards necessitates thorough understanding of regulations pertaining to materials usage, emissions limits, waste management, and more – all impacting the overall carbon footprint reduction efforts.
Addressing market challenges while promoting the value of environmentally conscious knee pads and reducing carbon dioxide equivalent emissions is essential for success in this space. Educating consumers about the importance of sustainability and highlighting the positive impact of choosing such products over traditional options helps build brand loyalty while contributing to broader environmental goals.
Summary
You’ve delved into the environmental impact of knee pad production, uncovering carbon footprint hotspots and exploring strategies for reduction. Innovative approaches and collaborative efforts have been highlighted, along with ethical considerations and the need for sustainable funding. Despite limitations, the journey towards sustainability in knee pad production, including carbon dioxide equivalent emissions and carbon footprint, is gaining momentum.
As you consider the broader implications of reducing carbon footprint in knee pad production, remember that every small change contributes to significant collective impact. Whether it’s advocating for sustainable practices or supporting eco-friendly initiatives, your actions matter. Embracing sustainability isn’t just about reducing carbon footprint; it’s about shaping a future where our choices safeguard the environment. Let’s continue this vital conversation and drive real change to reduce carbon dioxide equivalent emissions for a more sustainable tomorrow.
Frequently Asked Questions
How does knee pad production impact the environment?
Knee pad production impacts the environment through energy consumption, waste generation, and resource usage. The manufacturing process and transportation contribute to carbon emissions. By identifying these hotspots, companies can implement strategies for reducing their carbon footprint and equivalent emissions.
What are some innovative approaches in knee pad production that help reduce carbon footprint?
Innovative approaches such as using sustainable materials, implementing energy-efficient manufacturing processes, and optimizing supply chain logistics can significantly reduce the carbon footprint of knee pad production. These approaches not only benefit the environment but also reduce carbon dioxide equivalent emissions within the industry.
Are there collaborative efforts for sustainability in knee pad production?
Yes, many companies collaborate with environmental organizations, research institutions, and other stakeholders to develop sustainable practices in knee pad production. Collaborative efforts often lead to shared knowledge and resources that drive meaningful change toward reducing carbon footprint and equivalent emissions throughout the industry.
What ethical considerations should be taken into account in knee pad production for reducing carbon footprint?
Ethical considerations include fair labor practices, responsible sourcing of materials, and ensuring worker safety during manufacturing processes. Integrating ethical principles into every stage of production helps uphold social responsibility while striving to minimize environmental impact and carbon dioxide equivalent emissions.
How can funding support research for sustainability in knee pad production?
Funding plays a crucial role in supporting research initiatives aimed at developing innovative technologies and sustainable practices within knee pad production. It enables researchers to explore new methods for reducing carbon emissions while enhancing overall environmental performance.